ریختهگری پیوسته از فرآیندهای ارتباطی مهم بین فولادسازی و نورد است. از سال ۱۸۵۶ میلادی این روش برای ریختهگری پیشنهاد شد که در سال ۱۹۳۰ به عنوان روشی رایج برای تولید آلیاژهای غیرآهنی نیز مورد استفاده قرار گرفت. در اواسط دهه ۱۹۸۰، ریختهگری پیوسته به بزرگترین روش ریختهگری تبدیل شد و از مسیر ریختهگری فولاد شمش معمولی فراتر رفت. استفاده از ریختهگری پیوسته برای تولید شمش، مزایای مهمی از جمله بهبود کیفیت، عملکرد بهتر و صرفه جویی در انرژی و نیروی انسانی در مقابل دیگر روشها دارد. امروزه حدود %۹۵ فولاد جهان به روش ریختهگری پیوسته تولید میشود.
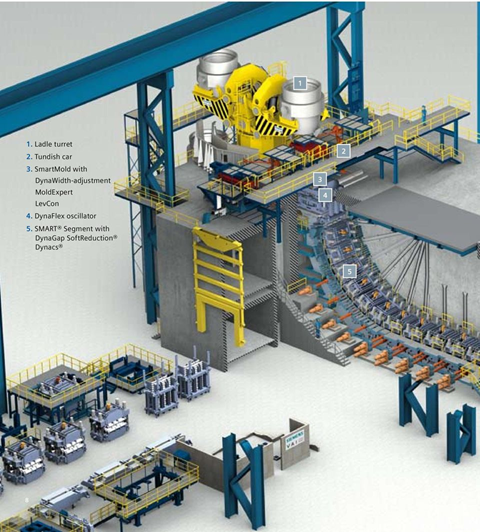
همانطور که در شکل ۱ مشاهده میشود، فرآیند ریختهگری پپیوسته مکانیزم سادهای دارد. مذاب با استفاده از پاتیل به خط CCM (Continuous Casting Machine) منتقل میشود. سپس با شروع فرآیند ذوب (با کنترل دبی) از پاتیل به تاندیش ریخته میشود و سپس از تاندیش از طریق SEN (Submerged Entry Nozzle، نازل غوطهور ورودی) به داخل قالبها هدایت میشود. قالبها معمولاً مسی و آبگرد هستند. اولین انجماد در فصل مشترک قالب-مذاب رخ میدهد و این ضخامت منجمد شده مرتباً با حرکت در طول مسیر افزایش مییابد. در سمت خروجی قالب، ضخامت لایه منجمد شده باید به حدی باشد تا بتواند مذاب داخل خود را خارج از قالب کنترل کند. سپس در زیر قالب قسمت منجمد شده با کمک پاشش آب، سرد میشود. در انتها، برشکاری انجام میگیرد تا به خط نورد منتقل شود. اصلیترین چالش در CCM، ریختهگری پیوسته بدون وقفه و انواع عیوب آن است. تمیزی فولاد به عملیات پاتیلی و تاندیش وابسته است. از جمله پارامترهای مهم برای کنترل تمیزی فولاد میتوان به ترکیب شیمیایی فولاد، سرعت ریختهگری، پودر قالب، نوسان قالب، دمای ذوب و شرایط خنککاری ثانویه اشاره کرد.
برای این منظور از LF (ladle furnace، کوره پاتیلی)در اکثر کارخانههای فولادسازی استفاده میشود. در این فرآیند تمام ملزومات متالورژی ثانویه به جز گاززدایی انجام میپذیرد. در شکل ۲ بخشهای مختلف فرآیند متالورژی ثانویه مشاهده میشود که به شرح زیر است:
- ماشین حمل و نقل که پاتیل ذوب روی آن قرار میگیرد.
- پاتیل حاوی ذوب و لایه سرباره بالای آن. سرباره به عنوان محافظ ذوب در برابر اتمسفر و جلوگیری از انتقال حرارت و کمک به تصفیه ذوب است.
- دمش گاز آرگون یا نیتروژن از کف برای همگن سازی و گوگردزدایی و شناورسازی آخال انجام میشود.
- دریچه آب خنککاری.
- بازوهای رسانا برق.
- مخزن و ماشین تزریق جهت افزودن عناصر آلیاژی در زمانی که مقدار ماده افزودنی کم باشد و یا فشار بخار آن بالاتر از دمای مذاب باشد.
- لنس برای نمونهبرداری و کنترل دما.
- سه الکترود برای ایجاد قوس الکتریکی و تنظیم حرارت مذاب.
شکل۲- شماتیک فرآیند متالورژي ثانویه.